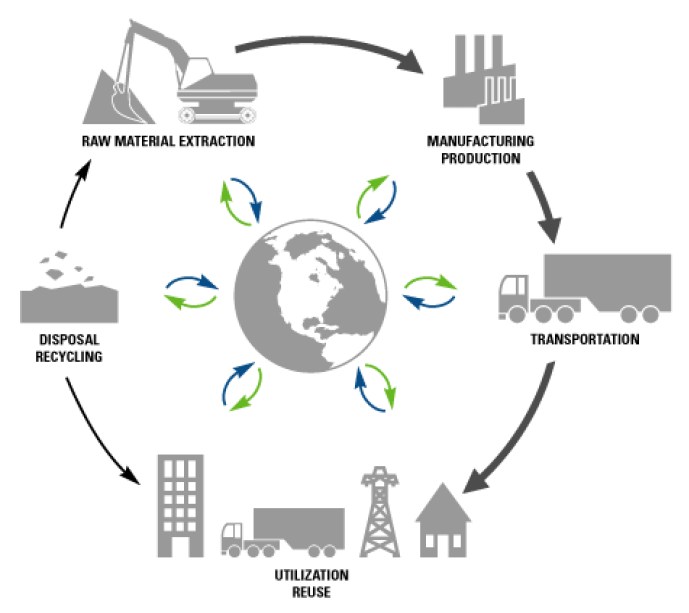
Tất cả thông tin cần biết về PLM-Quản lý vòng đời sản phẩm
Mục lục
Trong công nghiệp, quản lý vòng đời sản phẩm (PLM) là quá trình quản lý toàn bộ vòng đời của sản phẩm từ khi có ý tưởng, thông qua thiết kế kỹ thuật và sản xuất, đến dịch vụ và xử lý các sản phẩm được sản xuất. PLM tích hợp con người, dữ liệu, quy trình và hệ thống kinh doanh và cung cấp thông tin sản phẩm quan trọng cho các công ty và giúp họ mở rộng doanh nghiệp
Lịch sử
Cảm hứng cho quá trình kinh doanh đang phát triển được gọi là PLM đến từ Tập đoàn American Motors (AMC). Nhà sản xuất ô tô đang tìm cách đẩy nhanh quá trình phát triển sản phẩm của mình để cạnh tranh tốt hơn với các đối thủ lớn hơn vào năm 1985, theo ông François Castaing, Phó Chủ tịch Kỹ thuật và Phát triển Sản phẩm. [6] Thiếu “ngân sách khổng lồ của General Motors, Ford và các đối thủ nước ngoài, đã ra mắt thị trường xe thể thao đa dụng (SUV) hiện đại, AMC bắt đầu phát triển một mẫu xe mới, sau đó được ra mắt với tên gọi Jeep Grand Cherokee. Phần đầu tiên trong nhiệm vụ phát triển sản phẩm nhanh hơn là hệ thống phần mềm thiết kế hỗ trợ máy tính (CAD) giúp các kỹ sư làm việc hiệu quả hơn. Phần thứ hai trong nỗ lực này là hệ thống truyền thông mới cho phép giải quyết xung đột nhanh hơn, cũng như giảm các thay đổi kỹ thuật tốn kém vì tất cả các bản vẽ và tài liệu đều nằm trong cơ sở dữ liệu trung tâm. Việc quản lý dữ liệu sản phẩm hiệu quả đến mức sau khi AMC được Chrysler mua, hệ thống đã được mở rộng khắp doanh nghiệp kết nối mọi người tham gia thiết kế và xây dựng sản phẩm. Mặc dù sớm áp dụng công nghệ PLM, Chrysler đã có thể trở thành nhà sản xuất chi phí thấp nhất của ngành công nghiệp ô tô, ghi nhận chi phí phát triển chỉ bằng một nửa so với mức trung bình của ngành vào giữa những năm 1990.
Trong thời gian 1982-83, Rockwell International đã phát triển các khái niệm ban đầu về PDM và PLM cho chương trình máy bay ném bom B-1B. Hệ thống được gọi là Engineering Data System (EDS) đã được tăng cường để giao tiếp với các hệ thống Computervision và CADAM để theo dõi cấu hình bộ phận và vòng đời của các thành phần và cụm. Computervison sau đó đã phát hành chỉ thực hiện các khía cạnh PDM vì mô hình vòng đời là dành riêng cho Rockwell và nhu cầu hàng không vũ trụ.
Các loại hình
Các hệ thống PLM giúp các tổ chức đối phó với những thách thức ngày càng phức tạp và kỹ thuật trong việc phát triển các sản phẩm mới cho thị trường cạnh tranh toàn cầu.
Quản lý vòng đời sản phẩm (PLM) nên được phân biệt với ‘quản lý vòng đời sản phẩm (tiếp thị)’ (PLCM). PLM mô tả khía cạnh kỹ thuật của sản phẩm, từ việc quản lý các mô tả và tính chất của sản phẩm thông qua sự phát triển và tuổi thọ hữu ích của nó; trong khi đó, PLCM đề cập đến việc quản lý thương mại cuộc sống của một sản phẩm trong thị trường kinh doanh liên quan đến chi phí và các biện pháp bán hàng.
Quản lý vòng đời sản phẩm có thể được coi là một trong bốn nền tảng của cấu trúc công nghệ thông tin của một tập đoàn sản xuất. Tất cả các công ty cần quản lý thông tin liên lạc và thông tin với khách hàng của họ (quản lý quan hệ khách hàng CRM), nhà cung cấp và triển khai (quản lý chuỗi cung ứng SCM), tài nguyên của họ trong doanh nghiệp (lập kế hoạch nguồn lực doanh nghiệp ERP) và lập kế hoạch và phát triển sản phẩm ( PLM).
Một dạng của PLM được gọi là PLM lấy con người làm trung tâm. Mặc dù các công cụ PLM truyền thống chỉ được triển khai khi công bố hoặc trong giai đoạn hoàn thiện, PLM lấy người làm trung tâm nhắm vào giai đoạn thiết kế.
Kể từ năm 2009, phát triển CNTT-TT (dự án Promise do EU tài trợ 2004 ,2008) đã cho phép PLM vượt ra ngoài PLM truyền thống và tích hợp dữ liệu đo lường và ‘dữ liệu sự kiện vòng đời’ vào PLM, cũng như cho phép thông tin này được cung cấp cho những người chơi khác nhau trong tổng số vòng đời của một sản phẩm riêng lẻ (vòng lặp thông tin kín). Điều này đã dẫn đến việc mở rộng PLM thành quản lý vòng đời khép kín (CL2M).
Lợi ích
Các lợi ích được chỉ ra trong quản lý vòng đời sản phẩm bao gồm:
Giảm thời gian đưa ra thị trường
Bán sản phẩm được giá, đúng giá
Cải thiện chất lượng sản phẩm và độ tin cậy
Giảm chi phí tạo mẫu
Yêu cầu chính xác và kịp thời hơn để tạo báo giá
Khả năng nhanh chóng xác định các cơ hội bán hàng tiềm năng và đóng góp doanh thu
Tiết kiệm thông qua việc sử dụng lại dữ liệu gốc
Một khuôn khổ để tối ưu hóa sản phẩm
Giảm chất thải
Tiết kiệm thông qua việc tích hợp hoàn toàn các quy trình công việc kỹ thuật
Tài liệu có thể hỗ trợ chứng minh sự tuân thủ đối với RoHS hoặc Điều lệ 21 CFR Phần 11
Khả năng cung cấp cho các nhà sản xuất hợp đồng quyền truy cập vào một hồ sơ sản phẩm tập trung
Quản lý biến động theo mùa
Cải thiện dự báo để giảm chi phí nguyên vật liệu
Tối đa hóa sự hợp tác chuỗi cung ứng
Các Lĩnh vực của PLM
Trong PLM có năm lĩnh vực chính
Kỹ thuật hệ thống (SE) tập trung vào việc đáp ứng tất cả các yêu cầu, chủ yếu đáp ứng nhu cầu của khách hàng và điều phối quá trình thiết kế hệ thống bằng cách liên quan đến tất cả các ngành liên quan. Một khía cạnh quan trọng để quản lý vòng đời là một tập hợp con trong Kỹ thuật hệ thống được gọi là Kỹ thuật độ tin cậy.
Sản phẩm và danh mục đầu tư (PPM) tập trung vào việc quản lý phân bổ nguồn lực, theo dõi tiến độ, lập kế hoạch cho các dự án phát triển sản phẩm mới đang trong quá trình (hoặc trong tình trạng nắm giữ). Quản lý danh mục đầu tư là một công cụ hỗ trợ quản lý theo dõi tiến độtrên các sản phẩm mới và đưa ra quyết định đánh đổi khi phân bổ nguồn lực khan hiếm.
Thiết kế sản phẩm (CAx) là quá trình tạo ra một sản phẩm mới được bán bởi một doanh nghiệp cho khách hàng của mình.
Quản lý quy trình sản xuất (MPM) là một tập hợp các công nghệ và phương pháp được sử dụng để xác định cách sản xuất các sản phẩm.
Quản lý dữ liệu sản phẩm (PDM) tập trung vào việc nắm bắt và duy trì thông tin về các sản phẩm và / hoặc dịch vụ thông qua sự phát triển và cuộc sống hữu ích của chúng. Quản lý thay đổi là một phần quan trọng của PDM / PLM.
Lưu ý: Mặc dù phần mềm ứng dụng không bắt buộc đối với các quy trình PLM, độ phức tạp và tốc độ thay đổi kinh doanh đòi hỏi các tổ chức thực hiện càng nhanh càng tốt.
Giới thiệu về quá trình phát triển
Cốt lõi của PLM (quản lý vòng đời sản phẩm) là việc tạo và quản lý trung tâm tất cả dữ liệu sản phẩm và công nghệ được sử dụng để truy cập thông tin và kiến thức này. PLM như một chương trình xuất hiện từ các công cụ như CAD, CAM và PDM, nhưng có thể được xem là sự tích hợp của các công cụ này với các kỹ năng, con người và các quy trình thông qua tất cả các giai đoạn của vòng đời sản phẩm. Nó không chỉ là về công nghệ phần mềm mà còn là một chiến lược kinh doanh.
Quản lý vòng đời sản phẩm
Để đơn giản, các giai đoạn được mô tả được thể hiện trong quy trình kỹ thuật tuần tự truyền thống. Thứ tự chính xác của sự kiện và nhiệm vụ sẽ thay đổi tùy theo sản phẩm và ngành được đề cập nhưng các quy trình chính là:
Lên ý tưởng, thai nghén
Đặc điểm kỹ thuật
Thiết kế ý tưởng
Thiết kế
Thiết kế chi tiết
Xác nhận và phân tích (mô phỏng)
Thiết kế công cụ
Thực thi
Kế hoạch sản xuất
Sản xuất
Chế tạo / Lắp ráp
Kiểm tra (kiểm soát chất lượng)
Dịch vụ
Bán và giao hàng
Sử dụng
Duy trì và hỗ trợ
Vứt bỏ
Các sự kiện quan trọng chính là:
Nhận yêu cầu
Ý kiến
Bắt đầu
Đóng băng thiết kế
Phát hành, công bố
Tuy nhiên, thực tế phức tạp hơn, mọi người và các bộ phận không thể thực hiện các nhiệm vụ của mình một cách cô lập và một hoạt động không thể đơn giản kết thúc và hoạt động tiếp theo bắt đầu. Thiết kế là một quá trình lặp đi lặp lại, thường các thiết kế cần phải được sửa đổi do các ràng buộc sản xuất hoặc các yêu cầu mâu thuẫn. Việc một đơn đặt hàng của khách hàng có phù hợp với dòng thời gian hay không phụ thuộc vào loại ngành và liệu các sản phẩm đó có được sản xuất theo đơn đặt hàng, được thiết kế để đặt hàng hoặc lắp ráp để đặt hàng hay không.
Các giai đoạn của vòng đời sản phẩm và các công nghệ tương ứng
Nhiều giải pháp phần mềm đã được phát triển để tổ chức và tích hợp các giai đoạn khác nhau của vòng đời sản phẩm. PLM không nên được xem như là một sản phẩm phần mềm mà là một tập hợp các công cụ phần mềm và phương pháp làm việc được tích hợp với nhau để giải quyết các giai đoạn duy nhất của vòng đời hoặc kết nối các tác vụ khác nhau hoặc quản lý toàn bộ quy trình. Một số nhà cung cấp phần mềm bao gồm toàn bộ phạm vi PLM trong khi những nhà cung cấp ứng dụng thích hợp khác. Một số ứng dụng có thể trải rộng trên nhiều lĩnh vực PLM với các mô-đun khác nhau trong cùng một mô hình dữ liệu. Tổng quan về các lĩnh vực trong PLM được đề cập ở đây. Tuy nhiên, cần lưu ý rằng các phân loại đơn giản không phải lúc nào cũng phù hợp chính xác, nhiều khu vực chồng chéo và nhiều sản phẩm phần mềm bao gồm nhiều khu vực hoặc không dễ dàng phù hợp với một danh mục. Cũng không nên quên rằng một trong những mục tiêu chính của PLM là thu thập kiến thức có thể được sử dụng lại cho các dự án khác và phối hợp phát triển đồng thời nhiều sản phẩm. Đó là về các quy trình kinh doanh, con người và phương pháp nhiều như các giải pháp ứng dụng phần mềm. Mặc dù PLM chủ yếu liên quan đến các nhiệm vụ kỹ thuật, nó cũng liên quan đến các hoạt động tiếp thị như quản lý danh mục sản phẩm (PPM), đặc biệt liên quan đến phát triển sản phẩm mới (NPD). Có một số mô hình vòng đời trong ngành để xem xét, nhưng hầu hết đều khá giống nhau. Dưới đây là một mô hình vòng đời có thể; trong khi nó nhấn mạnh các sản phẩm định hướng phần cứng, các giai đoạn tương tự sẽ mô tả bất kỳ hình thức sản phẩm hoặc dịch vụ nào, bao gồm các sản phẩm phi kỹ thuật hoặc dựa trên phần mềm: [16]
Giai đoạn 1: Ý tưởng
Tưởng tượng, chỉ định, lập kế hoạch, đổi mới
Giai đoạn đầu tiên là định nghĩa về các yêu cầu sản phẩm dựa trên quan điểm của khách hàng, công ty, thị trường và cơ quan quản lý. Từ đặc điểm kỹ thuật này, các thông số kỹ thuật chính của sản phẩm có thể được xác định. Song song, công việc thiết kế khái niệm ban đầu được thực hiện xác định tính thẩm mỹ của sản phẩm cùng với các khía cạnh chức năng chính của nó. Nhiều phương tiện khác nhau được sử dụng cho các quy trình này, từ bút chì và giấy cho đến mô hình đất sét đến phần mềm thiết kế công nghiệp hỗ trợ máy tính 3D CAID.
Trong một số khái niệm, việc đầu tư nguồn lực vào nghiên cứu hoặc phân tích tùy chọn có thể được đưa vào giai đoạn thụ thai – ví dụ: đưa công nghệ đến mức trưởng thành đủ để chuyển sang giai đoạn tiếp theo. Tuy nhiên, kỹ thuật vòng đời là lặp đi lặp lại. Luôn luôn có khả năng một cái gì đó không hoạt động tốt trong bất kỳ phasđủ để sao lưu vào giai đoạn trước – có lẽ là tất cả các cách quay lại thụ thai hoặc nghiên cứu. Có rất nhiều ví dụ để rút ra.
Giai đoạn 2: Thiết kế
Mô tả, xác định, phát triển, kiểm tra, phân tích và xác nhận
Đây là nơi bắt đầu thiết kế và phát triển chi tiết của mẫu sản phẩm, tiến tới thử nghiệm nguyên mẫu, thông qua phát hành thử nghiệm để ra mắt sản phẩm đầy đủ. Nó cũng có thể liên quan đến thiết kế lại và đoạn đường nối để cải thiện các sản phẩm hiện có cũng như lỗi thời theo kế hoạch. [17] Công cụ chính được sử dụng để thiết kế và phát triển là CAD. Đây có thể là bản vẽ / phác thảo 2D đơn giản hoặc mô hình hóa dựa trên đặc tính / bề mặt 3D. Phần mềm này bao gồm các công nghệ như Mô hình lai, Kỹ thuật đảo ngược, KBE (kỹ thuật dựa trên kiến thức), NDT (thử nghiệm không phá hủy) và xây dựng lắp ráp.
Bước này bao gồm nhiều ngành kỹ thuật bao gồm: cơ khí, điện, điện tử, phần mềm (nhúng) và đặc thù miền, như kiến trúc, hàng không vũ trụ, ô tô, … Cùng với việc tạo ra hình học thực tế, có phân tích các thành phần và lắp ráp sản phẩm. Các nhiệm vụ mô phỏng, xác nhận và tối ưu hóa được thực hiện bằng phần mềm CAE (kỹ thuật hỗ trợ máy tính) hoặc được tích hợp trong gói CAD hoặc độc lập. Chúng được sử dụng để thực hiện các nhiệm vụ như: – Phân tích ứng suất, FEA (phân tích phần tử hữu hạn); động học; động lực học chất lỏng tính toán (CFD); và mô phỏng sự kiện cơ học (MES). CAQ (chất lượng hỗ trợ của máy tính) được sử dụng cho các nhiệm vụ như phân tích dung sai kích thước (kỹ thuật). Một nhiệm vụ khác được thực hiện trong giai đoạn này là tìm nguồn cung ứng các thành phần đã mua, có thể với sự trợ giúp của các hệ thống mua sắm.
Giai đoạn 3: Thực thi
Kế hoạch, sản xuất, xây dựng, vật tư, sản xuất, bán và giao hàng
Sau khi thiết kế các chi tiết của sản phẩm thành công, phương thức sản xuất được xác định. Điều này bao gồm các nhiệm vụ CAD như thiết kế công cụ; bao gồm cả việc tạo ra các hướng dẫn gia công CNC cho các bộ phận của sản phẩm cũng như tạo ra các công cụ cụ thể để sản xuất các bộ phận đó, sử dụng phần mềm CAM (sản xuất hỗ trợ máy tính) tích hợp hoặc riêng biệt. Điều này cũng sẽ liên quan đến các công cụ phân tích để mô phỏng quá trình các hoạt động như đúc, đúc và tạo khuôn ép. Khi phương thức sản xuất đã được xác định, CPM sẽ được sử dụng. Điều này liên quan đến các công cụ của CAPE (Computer Aided Production Engineering) hoặc CAP / CAPP (Computer Aided sản xuất) để thực hiện bố trí nhà máy, nhà máy và cơ sở và mô phỏng sản xuất, ví dụ mô phỏng dòng báo chí, công thái học công nghiệp, cũng như quản lý lựa chọn công cụ. Khi các thành phần được sản xuất, hình dạng và kích thước hình học của chúng có thể được kiểm tra đối với dữ liệu CAD gốc bằng cách sử dụng thiết bị và phần mềm kiểm tra có sự trợ giúp của máy tính. Song song với các nhiệm vụ kỹ thuật, công việc cấu hình sản phẩm bán hàng và tài liệu tiếp thị diễn ra. Điều này có thể bao gồm chuyển dữ liệu kỹ thuật (dữ liệu hình học và danh sách một phần) sang cấu hình bán hàng dựa trên web và các hệ thống xuất bản máy tính để bàn khác.
Giai đoạn 4: Dịch vụ
Sử dụng, vận hành, bảo trì, hỗ trợ, duy trì, loại bỏ, tái chế và xử lý
Giai đoạn cuối cùng của vòng đời liên quan đến việc quản lý thông tin “tại chỗ”. Điều này có thể bao gồm cung cấp cho khách hàng và kỹ sư dịch vụ sự hỗ trợ và thông tin cần thiết để sửa chữa và bảo trì, cũng như quản lý hoặc tái chế chất thải. Điều này có thể liên quan đến việc sử dụng các công cụ như phần mềm Bảo trì, Sửa chữa và Quản lý Vận hành (MRO).
Có một kết thúc cho mỗi sản phẩm. Cho dù đó là xử lý hoặc phá hủy các đối tượng hoặc thông tin vật chất, điều này cần phải được xem xét cẩn thận vì nó có thể được luật hóa và do đó không thoát khỏi sự phân nhánh.
Tất cả các giai đoạn: vòng đời sản phẩm
Giao tiếp, quản lý và cộng tác
Không có giai đoạn nào ở trên nên được coi là cô lập. Trong thực tế, một dự án không chạy tuần tự hoặc tách biệt với các dự án phát triển sản phẩm khác, với quy trình công việc giữa những người và hệ thống khác nhau. Một phần chính của PLM là sự phối hợp và quản lý dữ liệu định nghĩa sản phẩm. Điều này bao gồm quản lý thay đổi kỹ thuật và trạng thái phát hành của các thành phần; cấu hình biến thể sản phẩm; quản lý tài liệu; lập kế hoạch nguồn lực dự án cũng như thời gian và đánh giá rủi ro.
Đối với các tác vụ này, dữ liệu về đồ họa, văn bản và meta – chẳng hạn như Bảng kê Vật liệu (BOM) – cần phải được quản lý. Ở cấp độ bộ phận kỹ thuật, đây là mảng của phần mềm Quản lý dữ liệu sản phẩm (PDM) hoặc ở phần mềm Quản lý dữ liệu doanh nghiệp (EDM) ở cấp độ công ty; sự phân biệt mức độ cứng nhắc như vậy có thể không được sử dụng một cách nhất quán, tuy nhiên, thông thường sẽ thấy hai hoặc nhiều hệ thống quản lý dữ liệu trong một tổ chức. Các hệ thống này cũng có thể được liên kết với các hệ thống doanh nghiệp khác như SCM, CRM và ERP. Liên kết với các hệ thống này là các hệ thống quản lý dự án để lập kế hoạch dự án / chương trình.
Vai trò trung tâm này được bao phủ bởi nhiều công cụ phát triển sản phẩm hợp tác chạy suốt toàn bộ vòng đời và giữa các tổ chức. Điều này đòi hỏi nhiều công cụ công nghệ trong các lĩnh vực hội nghị, chia sẻ dữ liệu và dịch thuật dữ liệu. Lĩnh vực chuyên môn này được gọi là trực quan hóa sản phẩm bao gồm các công nghệ như DMU (mô phỏng kỹ thuật số), tạo mẫu kỹ thuật số ảo nhập vai (thực tế ảo) và hình ảnh siêu thực.
Kỹ năng người dùng
Mảng rộng các giải pháp tạo nên các công cụ được sử dụng trong bộ giải pháp PLM (ví dụ: CAD, CAM, CAx …) ban đầu được sử dụng bởi các học viên tận tâm đã đầu tư thời gian và công sức để đạt được các kỹ năng cần thiết. Các nhà thiết kế và kỹ sư đã làm việc kỳ diệu với các hệ thống CAD, các kỹ sư sản xuất trở thành người dùng CAM có tay nghề cao trong khi các nhà phân tích, quản trị viên và quản lý hoàn toàn làm chủ công nghệ hỗ trợ của họ. Tuy nhiên, để đạt được các lợi thế đầy đủ của PLM cần có sự tham gia của nhiều người có nhiều kỹ năng khác nhau từ khắp một doanh nghiệp mở rộng, mỗi doanh nghiệp đòi hỏi khả năng truy cập và vận hành trên đầu vào và đầu ra của những người tham gia khác.
Mặc dù việc sử dụng các công cụ PLM ngày càng dễ dàng, việc đào tạo chéo tất cả nhân sự trên toàn bộ bộ công cụ PLM đã không được chứng minh là thực tế. Tuy nhiên, giờ đây, những tiến bộ đang được thực hiện để giải quyết sự dễ sử dụng cho tất cả những người tham gia trong đấu trường PLM. Một tiến bộ như vậy là sự sẵn có của các giao diện người dùng cụ thể “vai trò”. Thông qua các giao diện người dùng (UI) phù hợp, các lệnh được trình bày cho người dùng phù hợp với chức năng và chuyên môn của họ.
Những kỹ thuật này bao gồm:
Quy trình kỹ thuật đồng thời
Kiểu dáng công nghiệp
Thiết kế dưới lên (Bottom–up)
Thiết kế trên xuống (Top-down)
Thiết kế hai đầu-giữa-giữa
Quy trình thiết kế tải trước
Thiết kế trong bối cảnh
Thiết kế mô-đun
NPD phát triển sản phẩm mới
Thiết kế DFSS cho Six Sigma
Thiết kế DFMA cho sản xuất / lắp ráp
Kỹ thuật mô phỏng kỹ thuật số
Thiết kế theo yêu cầu
Xác nhận quản lý đặc tả
Quản lý cấu hình
Quy trình kỹ thuật đồng thời
Kỹ thuật đồng thời (tiếng Anh Anh: kỹ thuật đồng thời) là một quy trình công việc, thay vì làm việc tuần tự qua các giai đoạn, thực hiện song song một số nhiệm vụ. Ví dụ: thiết kế công cụ bắt đầu ngay khi thiết kế chi tiết đã bắt đầu và trước khi thiết kế chi tiết của sản phẩm kết thúc; hoặc bắt đầu trên các mô hình rắn thiết kế chi tiết trước khi các mô hình thiết kế bề mặt khái niệm hoàn tất. Mặc dù điều này không nhất thiết làm giảm lượng nhân lực cần thiết cho một dự án, vì cần nhiều thay đổi hơn do thông tin không đầy đủ và thay đổi, nhưng nó làm giảm đáng kể thời gian dẫn và do đó thời gian đưa ra thị trường.
Các hệ thống CAD dựa trên tính năng trong nhiều năm đã cho phép hoạt động đồng thời trên mô hình rắn 3D và bản vẽ 2D bằng hai tệp riêng biệt, với bản vẽ nhìn vào dữ liệu trong mô hình; khi mô hình thay đổi bản vẽ sẽ cập nhật kết hợp. Một số gói CAD cũng cho phép sao chép kết hợp hình học giữa các tệp. Điều này cho phép, ví dụ, sao chép một thiết kế bộ phận vào các tệp được sử dụng bởi nhà thiết kế công cụ. Kỹ sư sản xuất sau đó có thể bắt đầu làm việc trên các công cụ trước khi thiết kế cuối cùng đóng băng; khi một thiết kế thay đổi kích thước hoặc hình dạng, hình dạng công cụ sẽ cập nhật. Kỹ thuật đồng thời cũng có thêm lợi ích là cung cấp giao tiếp tốt hơn và ngay lập tức hơn giữa các bộ phận, giảm cơ hội thay đổi thiết kế muộn, tốn kém. Nó áp dụng một phương pháp phòng ngừa vấn đề so với phương pháp giải quyết vấn đề và thiết kế lại của kỹ thuật tuần tự truyền thống.
Thiết kế Bottom-Up
Thiết kế dưới lên (CAD-centric) xảy ra khi định nghĩa mô hình 3D của sản phẩm bắt đầu bằng việc xây dựng các thành phần riêng lẻ. Những thứ này sau đó hầu như được kết hợp thành các cụm phụ của nhiều cấp cho đến khi toàn bộ sản phẩm được xác định kỹ thuật số. Điều này đôi khi được gọi là “cấu trúc đánh giá” cho thấy sản phẩm sẽ trông như thế nào. BOM chứa tất cả các thành phần vật lý (rắn) của sản phẩm từ hệ thống CAD; nó cũng có thể (nhưng không phải luôn luôn) chứa ‘các mặt hàng số lượng lớn’ khác cần thiết cho sản phẩm cuối cùng nhưng mặc dù (mặc dù có khối lượng và khối lượng vật lý xác định) thường không được liên kết với hình học CAD như sơn, keo, dầu, băng dính và vật liệu khác.
Thiết kế dưới lên có xu hướng tập trung vào các khả năng của công nghệ vật lý trong thế giới thực có sẵn, thực hiện các giải pháp mà công nghệ này phù hợp nhất. Khi các giải pháp đáy này lên có giá trị trong thế giới thực, thiết kế dưới đáy có thể hiệu quả hơn nhiều so với thiết kế xuống trên. Rủi ro của thiết kế đáy lên là nó cung cấp giải pháp rất hiệu quả cho các vấn đề giá trị thấp. Trọng tâm của thiết kế dưới cùng là “chúng ta có thể làm gì hiệu quả nhất với công nghệ này?” thay vì trọng tâm của top trên xuống, đó là “Điều đáng giá nhất để làm là gì?”
Thiết kế trên xuống
Thiết kế hàng đầu xuống được tập trung vào các yêu cầu chức năng cấp cao, với sự tập trung tương đối ít hơn vào công nghệ triển khai hiện có. Một thông số kỹ thuật cấp cao nhất được phân tách nhiều lần thành các cấu trúc và thông số kỹ thuật cấp thấp hơn, cho đến khi thực hiện vật lýlớp ation đạt được. Rủi ro của một thiết kế xuống hàng đầu là nó có thể không tận dụng các ứng dụng hiệu quả hơn của công nghệ vật lý hiện tại, do các lớp trừu tượng quá mức do đi theo một con đường trừu tượng không phù hợp với các thành phần có sẵn, ví dụ chỉ định riêng các yếu tố cảm biến, xử lý và truyền thông không dây mặc dù có thể có sẵn một thành phần phù hợp kết hợp các yếu tố này. Giá trị tích cực của thiết kế hàng đầu xuống là nó duy trì sự tập trung vào các yêu cầu giải pháp tối ưu.
Thiết kế trên xuống có thể loại bỏ một số rủi ro của thiết kế dưới lên. Điều này bắt đầu với một mô hình bố cục, thường là một bản phác thảo 2D đơn giản xác định kích thước cơ bản và một số tham số xác định chính, có thể bao gồm một số yếu tố thiết kế Công nghiệp. Hình học từ đây được sao chép một cách kết hợp xuống cấp độ tiếp theo, đại diện cho các hệ thống con khác nhau của sản phẩm. Hình học trong các hệ thống phụ sau đó được sử dụng để xác định chi tiết hơn ở các cấp độ bên dưới. Tùy thuộc vào độ phức tạp của sản phẩm, một số cấp độ của lắp ráp này được tạo ra cho đến khi định nghĩa cơ bản của các bộ phận có thể được xác định, chẳng hạn như kích thước vị trí và kích thước chính. Thông tin này sau đó được sao chép một cách kết hợp vào các tệp thành phần. Trong các tập tin này, các thành phần được chi tiết; đây là nơi bắt đầu lắp ráp cổ điển dưới lên.
Việc lắp ráp hàng đầu xuống đôi khi được gọi là “cấu trúc điều khiển”. Nếu một tệp duy nhất được sử dụng để xác định bố cục và tham số cho cấu trúc xem xét, nó thường được gọi là tệp khung.
Theo truyền thống, kỹ thuật quốc phòng phát triển cấu trúc sản phẩm từ trên xuống. Quy trình kỹ thuật hệ thống quy định phân rã chức năng các yêu cầu và sau đó phân bổ vật lý cấu trúc sản phẩm cho các chức năng. Cách tiếp cận từ trên xuống này thường sẽ có các mức thấp hơn của cấu trúc sản phẩm được phát triển từ dữ liệu CAD dưới dạng cấu trúc hoặc thiết kế dưới lên.
Thiết kế giữa và cuối
Thiết kế giữa và cuối (BEATM) là một quy trình thiết kế nhằm nỗ lực kết hợp các tính năng tốt nhất của thiết kế hàng đầu xuống và thiết kế dưới lên thành một quy trình. Luồng quy trình thiết kế BEATM có thể bắt đầu bằng một công nghệ mới nổi, đề xuất các giải pháp có thể có giá trị hoặc có thể bắt đầu với quan điểm hàng đầu về một vấn đề quan trọng cần giải pháp. Trong cả hai trường hợp, thuộc tính quan trọng của phương pháp thiết kế BEATM là tập trung ngay lập tức vào cả hai đầu của quy trình thiết kế: một cái nhìn từ trên xuống về các yêu cầu giải pháp và một cái nhìn từ dưới lên về công nghệ có sẵn có thể hứa hẹn về hiệu quả dung dịch. Quá trình thiết kế BEATM tiến hành từ cả hai đầu để tìm kiếm sự hợp nhất tối ưu ở đâu đó giữa các yêu cầu hàng đầu xuống và thực hiện hiệu quả từ dưới lên. Theo cách này, BEATM đã được chứng minh là thực sự cung cấp tốt nhất cả hai phương pháp. Thật vậy, một số câu chuyện thành công hay nhất từ đầu xuống hoặc xuống dưới đã trở nên thành công nhờ sử dụng phương pháp BEATM trực quan nhưng vô thức. Khi được sử dụng một cách có ý thức, BEATM cung cấp những lợi thế thậm chí còn mạnh mẽ hơn.
Thiết kế tải phía trước và quy trình làm việc
Tải trước đang đưa thiết kế hàng đầu xuống giai đoạn tiếp theo. Cấu trúc điều khiển hoàn chỉnh và cấu trúc xem xét, cũng như dữ liệu xuôi dòng như bản vẽ, phát triển công cụ và mô hình CAM, được xây dựng trước khi sản phẩm được xác định hoặc khởi động dự án đã được cho phép. Các tập hợp các tệp này tạo thành một mẫu mà từ đó một họ các sản phẩm có thể được xây dựng. Khi quyết định được đưa ra với một sản phẩm mới, các thông số của sản phẩm được nhập vào mô hình mẫu và tất cả các dữ liệu liên quan được cập nhật. Rõ ràng các mô hình liên kết được xác định trước sẽ không thể dự đoán tất cả các khả năng và sẽ yêu cầu công việc bổ sung. Nguyên tắc chính là rất nhiều công việc thử nghiệm / điều tra đã được hoàn thành. Rất nhiều kiến thức được tích hợp vào các mẫu này để được sử dụng lại trên các sản phẩm mới. Điều này không đòi hỏi các nguồn lực bổ sung “lên phía trước” nhưng có thể giảm đáng kể thời gian giữa khởi động dự án và khởi động. Tuy nhiên, các phương pháp như vậy đòi hỏi phải thay đổi tổ chức, vì những nỗ lực kỹ thuật đáng kể được chuyển sang các bộ phận phát triển “ngoại tuyến”. Nó có thể được coi là tương tự để tạo ra một chiếc xe ý tưởng để thử nghiệm công nghệ mới cho các sản phẩm trong tương lai, nhưng trong trường hợp này, công việc được sử dụng trực tiếp cho thế hệ sản phẩm tiếp theo.
Thiết kế theo bối cảnh
Các thành phần riêng lẻ không thể được xây dựng trong sự cô lập. Các mô hình CAD và CAID của các thành phần được tạo trong bối cảnh của một số hoặc tất cả các thành phần khác trong sản phẩm đang được phát triển. Điều này đạt được bằng cách sử dụng các kỹ thuật mô hình lắp ráp. Hình học của các thành phần khác có thể được nhìn thấy và được tham chiếu trong công cụ CAD đang được sử dụng. Các thành phần được tham chiếu khác có thể hoặc không được tạo bằng cùng một công cụ CAD, với hình dạng của chúng được dịch từ các định dạng phát triển sản phẩm hợp tác (CPD) khác. Một số kiểm tra lắp rápchẳng hạn như DMU cũng được thực hiện bằng phần mềm trực quan hóa sản phẩm.
Quản lý vòng đời sản phẩm và quy trình (PPLM)
Quản lý vòng đời sản phẩm và quy trình (PPLM) là một thể loại PLM thay thế, trong đó quá trình sản phẩm được tạo ra cũng quan trọng như chính sản phẩm. Thông thường, đây là khoa học đời sống và thị trường hóa chất đặc biệt tiên tiến. Quá trình đằng sau việc sản xuất một hợp chất nhất định là một yếu tố chính của việc nộp đơn quy định cho một ứng dụng thuốc mới. Do đó, PPLM tìm cách quản lý thông tin xung quanh sự phát triển của quy trình theo cách tương tự mà PLM nói về việc quản lý thông tin xung quanh việc phát triển sản phẩm.
Một biến thể của việc triển khai PPLM là Hệ thống thực thi phát triển quy trình (PDES). Họ thường thực hiện toàn bộ chu trình phát triển của sự phát triển công nghệ sản xuất công nghệ cao, từ quan niệm ban đầu, cho đến phát triển và sản xuất. PDES tích hợp mọi người với các nền tảng khác nhau từ các thực thể pháp lý, dữ liệu, thông tin và kiến thức và quy trình kinh doanh khác nhau.
Quy mô thị trường
Tổng chi tiêu cho phần mềm và dịch vụ PLM được ước tính trong năm 2006 là trên 30 tỷ đô la mỗi năm. [19] [20]
Sau cuộc Đại suy thoái, các khoản đầu tư của PLM từ năm 2010 trở đi cho thấy tốc độ tăng trưởng cao hơn so với hầu hết chi tiêu CNTT nói chung. [21]
Kim tự tháp của hệ thống sản xuất
Kim tự tháp của hệ thống sản xuất
Theo Malakooti (2013), [22] có năm mục tiêu dài hạn cần được xem xét trong các hệ thống sản xuất:
Chi phí: Có thể được đo lường theo đơn vị tiền tệ và thường bao gồm chi phí cố định và chi phí biến đổi.
Năng suất: Có thể được đo lường về số lượng sản phẩm được sản xuất trong một khoảng thời gian.
Chất lượng: Có thể được đo lường về mức độ hài lòng của khách hàng chẳng hạn.
Tính linh hoạt: Có thể coi là khả năng của hệ thống để sản xuất nhiều loại sản phẩm chẳng hạn.
Tính bền vững: Có thể được đo lường về mặt sinh thái, tức là tác động sinh học và môi trường của một hệ thống sản xuất.
Mối quan hệ giữa năm đối tượng này có thể được trình bày dưới dạng kim tự tháp với đỉnh của nó liên quan đến Chi phí thấp nhất, Năng suất cao nhất, Chất lượng cao nhất, Tính linh hoạt nhất và Tính bền vững cao nhất. Các điểm bên trong kim tự tháp này được liên kết với các kết hợp khác nhau của năm tiêu chí. Đầu của kim tự tháp đại diện cho một hệ thống lý tưởng (nhưng có khả năng rất khó khả thi) trong khi cơ sở của kim tự tháp đại diện cho hệ thống tồi tệ nhất có thể.