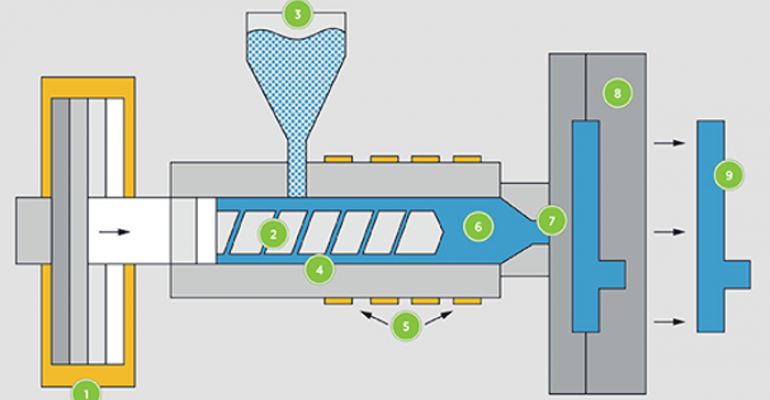
Công nghệ ép phun nhanh RIM-Rapid Injection Molding là gì?
Thiết kế các chi tiết bằng nhựa có thể đúc luôn luôn quan trọng đối với các quy trình ép phun truyền thống, nhưng nó đặc biệt có lợi cho các chi tiết sắp được đúc nhanh (RIM) để đảm bảo tốc độ và chất lượng không đổi trong quá trình sản xuất. Dưới đây, một cái nhìn về nhiều cân nhắc thiết kế quan trọng gặp phải trong quá trình ép phun nhanh
Ép phun nhanh
Với RIM, các mô hình CAD được gửi trực tiếp đến sàn sản xuất nơi bắt đầu phay khuôn. Trong hầu hết các trường hợp, khuôn được chế tạo từ nhôm, không phải thép. Điều này cho phép dụng cụ nhanh hơn và tiết kiệm chi phí hơn so với khuôn thép truyền thống.
RIM cung cấp các lõi mặt bên và tải bằng tay, cũng như ép xung và insert khuôn đơn giản. Sử dụng có chọn lọc gia công phóng điện (EDM) có thể cải thiện các tính năng khuôn như góc và cạnh. Và một số tùy chọn chất lượng bề mặt có sẵn. Tất cả điều này cho phép RIM sản xuất các chi tiết trong một vài tuần thay vì các tháng cần thiết cho các phương pháp ép phun truyền thống.
Từ trái sang phải, các thành phần của máy ép RIM bao gồm: ram (1), vít (2), phễu (3), thùng (4), lò sưởi (5), vật liệu (6), vòi phun (7), khuôn ( 8), và chi tiết (9).
Dưới đây là một số ứng dụng phổ biến cho RIM:
Lặp lại nhanh chóng với các nguyên mẫu được xây dựng nhanh chóng
Kiểm tra chức năng trong quá trình phát triển sản phẩm với các chi tiết cấp sản xuất
Kiểm tra một số vật liệu khác nhau
Kiểm tra một số mô hình CAD
Thực hiện dụng cụ cầu
Tận dụng sản xuất khối lượng thấp cho các chi tiết theo yêu cầu
Quản lý biến động nhu cầu
Nhận hàng ngàn phần trong vài ngày
Tính năng chi tiết cho RIM
Từ độ dày của thành và bán kính cho đến đường dốc và gân tăng cứng, ở đây, hãy xem xét nhanh các yếu tố mà các nhà thiết kế và kỹ sư nên xem xét nếu các chi tiết sẽ được đúc.
Độ dày của thành: Yêu cầu thiết kế quan trọng nhất để có được các chi tiết đúc tốt là duy trì độ dày thành không đổi. Chúng giảm thiểu khả năng cho các chi tiết bị cong vênh hoặc biến dạng.
Lưu ý: Đây là những hướng dẫn chung, tùy thuộc vào hình dạng chi tiết và cấu trúc đúc. Các chi tiết lớn hơn nên được thiết kế với độ dày thành tối thiểu. Quy tắc chung của Protolabs cho độ dày của thành là 0,040 đến 0,140 in.
Hình học lõi-Core Geometry: Lõi ra các chi tiết để loại bỏ các bức thành dày. Bạn có được các chức năng tương tự trong chi tiết đúc tốt. Độ dày không cần thiết có thể thay đổi kích thước chi tiết, giảm cường độ và yêu cầu gia công sau quá trình.
Phần bên trái là phần được thiết kế ban đầu. Phần bên phải đã được cắt ra để giảm độ dày của phần trong khi vẫn có thể thực hiện tất cả các chức năng cần thiết của nó.
Mặt dốc: Loại bỏ các cạnh sắc gây ra ứng suất khi đúc.
Fillet (Bo): Thiết kế các tính năng hỗ trợ
Bán kính: Các góc nhọn làm suy yếu các chi tiết và tạo ra ứng suất đúc từ dòng chảy nhựa. Nhà thiết kế nên thêm bán kính ở các góc nhọn.
Gân tăng cứng: Để chống lõm xuống, gân tăng cứng phải không quá 60% độ dày của thành.
Các vấu lồi: Không tạo ra các phần dày với vấu để vặn vít vì các phần dày có thể gây ra vết lõm và các khoảng trống trong chi tiết của bạn.
Các vấu lồi bên trái rất kém vì chúng quá dày và có thể không lấp đầy hoàn toàn, để lại những khoảng trống. Các ông chủ bên phải, tuy nhiên, tạo ra độ bền mà không có phần quá dày.
Góc nghiêng: Góc nghiêng (độ dốc so với các thành thẳng đứng) càng nhiều càng tốt để giúp đẩy ra các chi tiết dễ dàng hơn mà không cần dùng lưỡi đẩy hoặc thanh đẩy. Góc nghiêng cũng cho phép các nhà thiết kế tạo ra các tính năng sâu hơn, cộng với nó làm giảm các rỗ khí và các khuyết điểm mỹ phẩm khi phay các thành sâu. Nếu bạn có thể thêm phần vát thi nên từ 1 độ trở lên. Trên thiết kế lõi-lòng khuôn, sử dụng 2 độ. hoặc hơn. Một kinh nghiệm là 1 độ cho mỗi 2inch trong chiều sâu đầu tiên. Độ sâu từ 2 đến 4 in, thì lấy 3 độ. góc nghiêng tối thiểu là 1/8 in. Độ dày có thể được yêu cầu.
Core-Cavity: Khi bạn phác thảo, sử dụng lõi-lòng khuôn thay vì gân tăng cứng. Nó cung cấp độ dày thành không đổi thay vì các bức thành với một đế dày. Nó cũng cho phép các máy phay gia công khuôn có bề mặt tốt hơn và cung cấp các chi tiết tốt hơn nhanh hơn.
Undercuts: Undercut là một khu vực của chi tiết che phủ một khu vực khác của chi tiết, tạo ra một khóa liên động giữa chi tiết và một hoặc cả hai nửa khuôn. Trên hình ảnh bên dưới, hình ảnh bên trái (1) minh họa một clip có tính năng undercut. Trên hình ảnh bên phải (2), một lỗ truy cập bên dưới undercut cho phép khuôn nhô ra qua phần và cung cấp hình học ngắt chốt cần thiết.
Side-Actions ( lõi mặt bên) Cơ cấu tác động bên dưới bên ngoài chi tiết. Các undercut phải được bật hoặc kết nối với đường phân khuôn. Chúng cũng phải nằm trong mặt phẳng của đường phân khuôn và được nối và vuông góc với hướng mà khuôn đang mở.
Phần màu xanh tròn là lõi mặt bên.
Bumpoffs: Một cú va chạm là một đường cắt nhỏ trong thiết kế chi tiết có thể được gỡ bỏ an toàn khỏi khuôn kéo thẳng mà không cần sử dụng các lõi mặt bên. Bumpoffs có thể giải quyết một số undercut đơn giản, nhưng nhạy cảm với hình học và vật liệu.
Phần màu xanh lá cây là phần va chạm.
Pickout: Pickout là một miếng kim loại riêng biệt được đưa vào khuôn để tạo một undercut. Nó được đẩy ra với chi tiết, sau đó được người vận hành gỡ bỏ và lắp lại vào khuôn. Sử dụng một lựa chọn cho phép các nhà thiết kế vượt qua các hạn chế về hình dạng và định vị, nhưng tốn kém hơn so với lõi trượt hoặc sử dụng lõi mặt bên.
Chân lõi thép: Những lỗ này có thể được làm bằng chân lõi thép trong khuôn. Một chốt thép đủ bền để xử lý sự căng thẳng của việc phóng ra và đủ trơn tru để giải phóng sạch khỏi chi tiết mà không cần bản nháp. Không nên có bất kỳ hiệu ứng mỹ phẩm trên phần kết quả; nếu có, nó sẽ ở bên trong cái lỗ mà nó thắng được nhìn thấy.
Logo à chữ: Bề mặt có kết cấu, số phần được đúc và logo công ty trông đẹp, nhưng được chuẩn bị để trả thêm một chút cho các tính năng quan trọng không phải nhiệm vụ này. Điều đó nói rằng, số phần vĩnh viễn là yêu cầu cho nhiều ứng dụng hàng không vũ trụ và quân sự. Đối với văn bản, nó được khuyến khích thiết kế:
w Sử dụng phông chữ thân thiện với máy phay (phông chữ san-serif) như Century Gothic Bold, Arial hoặc Verdana.
w Giữ phông chữ trên 20 pt.
w Không sâu hơn 0,010 đến 0,015 in.
w Hãy tăng góc nghiêng nếu sợ khó khăn khi tách khuôn
Miệng phun: Các cạnh mỏng hạn chế dòng chảy và có thể bị vỡ trong quá trình cắt cổng. Cổng Tab cung cấp cho các nhà đúc khuôn một khu vực dày để đặt một cổng vào phần của bạn. Có thể có các lựa chọn thay thế, vì vậy vui lòng liên hệ với các kỹ sư
Các chi tiết tự lắp: Các chi tiết giống hệt nhau có thể lật và lắp với chính chúng là có thể và tiết kiệm chi phí của khuôn thứ hai. Các yếu tố để cho chúng lắp nối bao gồm chốt và lỗ, vành lồng vào nhau, và móc và chốt.
Dung sai: Các máy đúc thường có thể giữ khoảng ± 0,003 in. Độ chính xác gia công. Dung sai co ngót phụ thuộc chủ yếu vào thiết kế chi tiết và lựa chọn nhựa. Nó thay đổi từ 0,002 in./in. đối với các loại nhựa ổn định như ABS và polycarbonate đến 0,025 in./in. đối với các loại nhựa không ổn định như TPE. Có các kỹ thuật để có được độ chính xác cao nhất của ép phun. Liên hệ với một kỹ sư ứng dụng tại máy hàn của bạn để biết thêm thông tin.
Lựa chọn vật liệu
Khi chọn vật liệu cho một chi tiết, các đặc tính liên quan có thể bao gồm kháng cơ học, vật lý, hóa học, nhiệt, điện, dễ cháy và chống tia cực tím. Các nhà sản xuất nhựa, hợp chất và công cụ tìm kiếm nhựa độc lập có dữ liệu trực tuyến. Dưới đây là một cái nhìn nhanh chóng về một số loại nhựa kỹ thuật và hàng hóa phổ biến.
Nhựa tiêu dùng
Polypropylen
Mềm mại
Khó khăn
Giá rẻ
Kháng hóa chất
Làm cho bản lề sống tốt
Polyetylen
Mềm mại
Bền
Giá rẻ
Kháng hóa chất
Mật độ cao
Mật độ thấp
Polystyren
Cứng
Thông thoáng
Giá rẻ
Giòn nhưng có thể được tăng cứng
Nhựa kỹ thuật
ABS
Ít tốn kém
Chống va đập
Thiết bị và vỏ cầm tay
Dễ bị vênh
Acet
Đắt hơn
Bền
Độ bôi trơn tốt và khả năng gia công
Rất nhạy cảm với độ dày thành quá mức
LCP
Rất đắt
Rất bền
Lấp đầy những phần rất mỏng
Đường hàn yếu
Nylon
Chi phí hợp lý
Rất bền
Dễ bị co lại và cong vênh, đặc biệt là đầy thủy tinh
Hấp thụ nước, dẫn đến thay đổi kích thước và tính chất
Polycarbonate
Chi phí vừa phải
Rất bền
Độ chính xác kích thước tốt
Dễ bị nứt hóa học, lỗ rỗng
Các loại nhựa kỹ thuật khác bao gồm PBT, PET, PPS, PSU, PES và PEI.
Chọn chất màu: Màu sắc từ nhà cung cấp nhựa thường là màu đen và tự nhiên. Tự nhiên có thể là màu trắng, màu be, màu hổ phách hoặc màu khác. Màu bán tùy chỉnh được tạo ra khi các viên màu được thêm vào nhựa tự nhiên. Đối với màu sắc có sẵn, kiểm tra với máy hàn ép phun của bạn. Trong một số trường hợp, chẳng hạn như tại Protolabs, không có phí bổ sung cho màu sắc hàng tồn kho của chúng tôi. Nhưng chúng có thể không phải là một kết hợp chính xác và có thể tạo ra các vệt hoặc xoáy trong các phần. Các màu tùy chỉnh cần khớp với một Pantone chính xác hoặc chip màu cần được kết hợp với một nhà cung cấp nhựa. Quá trình này chậm hơn và tốn kém hơn, nhưng tạo ra một kết hợp chính xác hơn.
Phụ gia nhựa
Sợi thủy tinh ngắn có thể được thêm vào nhựa để tăng cường hỗn hợp và giảm leo, đặc biệt là ở nhiệt độ cao hơn. Chúng làm cho nhựa cứng hơn, cứng hơn và giòn hơn. Chúng cũng có thể gây cong vênh do sự khác biệt trong làm mát co lại giữa nhựa và sợi.
Sợi thủy tinh dài được sử dụng như sợi thủy tinh ngắn để tăng cường và giảm độ rão, nhưng làm cho nhựa cứng hơn và cứng hơn nhiều. Nhược điểm là chúng có thể đặc biệt khó khăn khi đúc các chi tiết có thành mỏng và / hoặc dòng nhựa dài.
Sợi Aramid (Kevlar) giống như sợi thủy tinh ít bị mài mòn, chỉ không bền bằng.
Sợi carbon tăng cường và / hoặc làm cứng một hỗn hợp và hỗ trợ trong việc tản tĩnh. Nó có những hạn chế tương tự như sợi thủy tinh. Sợi carbon có thể làm cho nhựa rất cứng.
Sợi thép không gỉ được sử dụng để điều khiển EMI (nhiễu điện từ) và RFI (nhiễu tần số vô tuyến) thường trong vỏ cho các linh kiện điện tử. Chúng dẫn điện nhiều hơn sợi carbon.
Các khoáng chất như Talc và đất sét thường được sử dụng làm chất độn để giảm chi phí hoặc tăng độ cứng của thành phẩm. Bởi vì chúng không co lại nhiều như nhựa làm khi coo dẫn, họ có thể giảm cong vênh.
PTFE (Teflon) và molybdenum disulfide được sử dụng để làm cho các chi tiết tự bôi trơn trong các ứng dụng ổ trục.
Hạt thủy tinh và mảnh mica làm cứng hỗn hợp và giảm cong vênh và co ngót. Với tải cao, chúng có thể là thách thức để ép phun.
Chất ức chế tia cực tím ngăn chặn các chi tiết phá vỡ dưới ánh sáng mặt trời cho các ứng dụng ngoài trời.